Orbis
December - July 2023
At Orbis, I was one of two full time mechanical engineers. I had to hit the ground running, learn quickly, and take ownership of many projects, which was a fantastic opportunity. I thrived in this fast paced environment, leading design on a planetary gearset retrofit project for an electric-converted McLaren MP4-12C, an integrated gearbox/motor/upright assembly, a hybrid battery mounting solution, and the optimization of an external brake rotor/”bell.”
I learned a lot at Orbis - one of the skills I was able to improve on the most was designing for manufacturing. I was in constant communication with Scott, the machinist and a co-founder of the company - I frequently asked him questions about how to make a part more machinable.
Planetary Gearset Retrofit
Requirements
- Reduce operating NVH
- Extreme timeline
- New gearset must fit within existing assembly and use existing splines
- Cost effective
My contributions
- Solely responsible for retrofit design and management
- Sourced gearset and worked directly
- with our machinist to make parts
- Tested NVH reduction with sound level meter
- Fitted to McLaren MP4-12C chassis
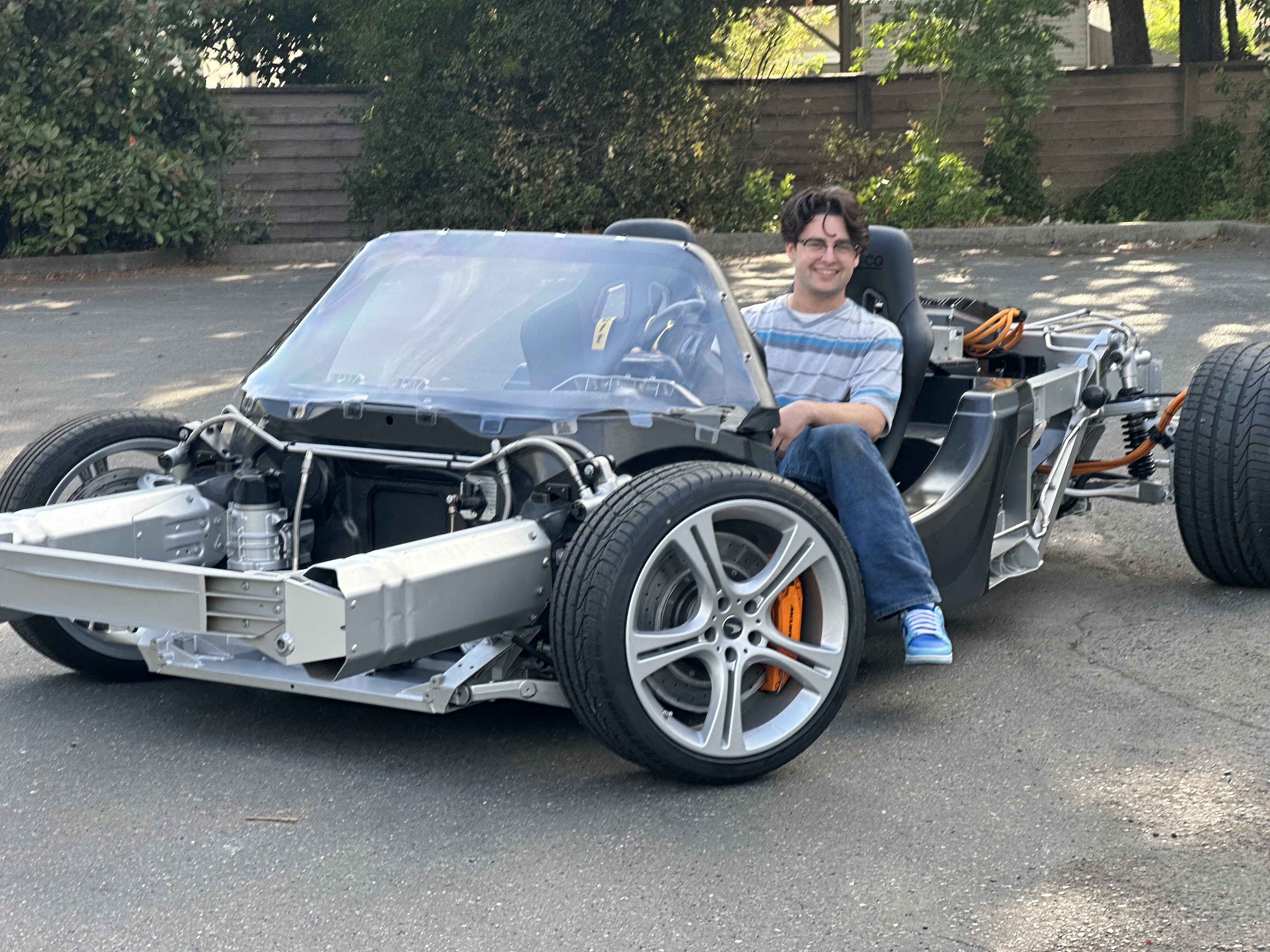
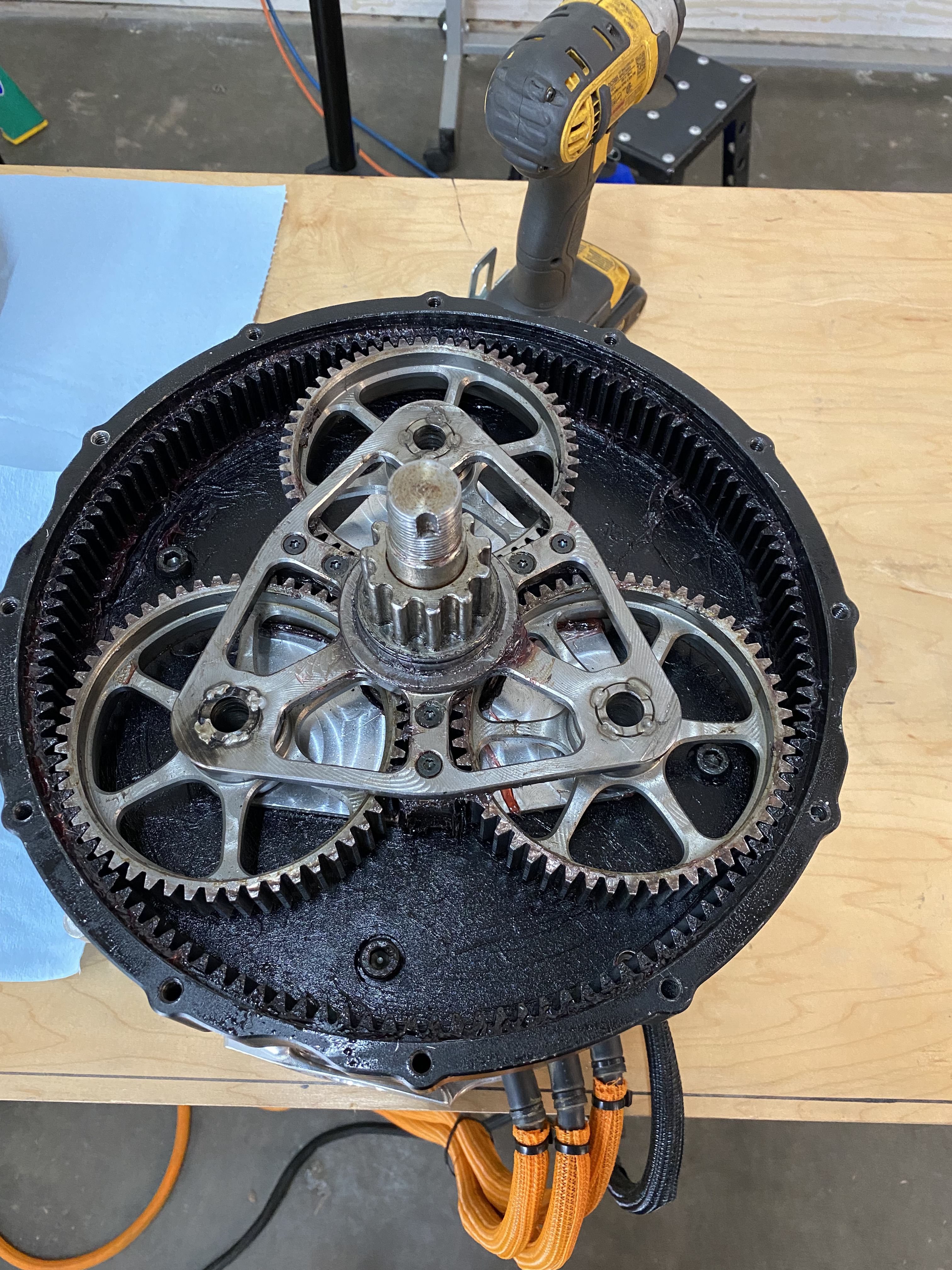
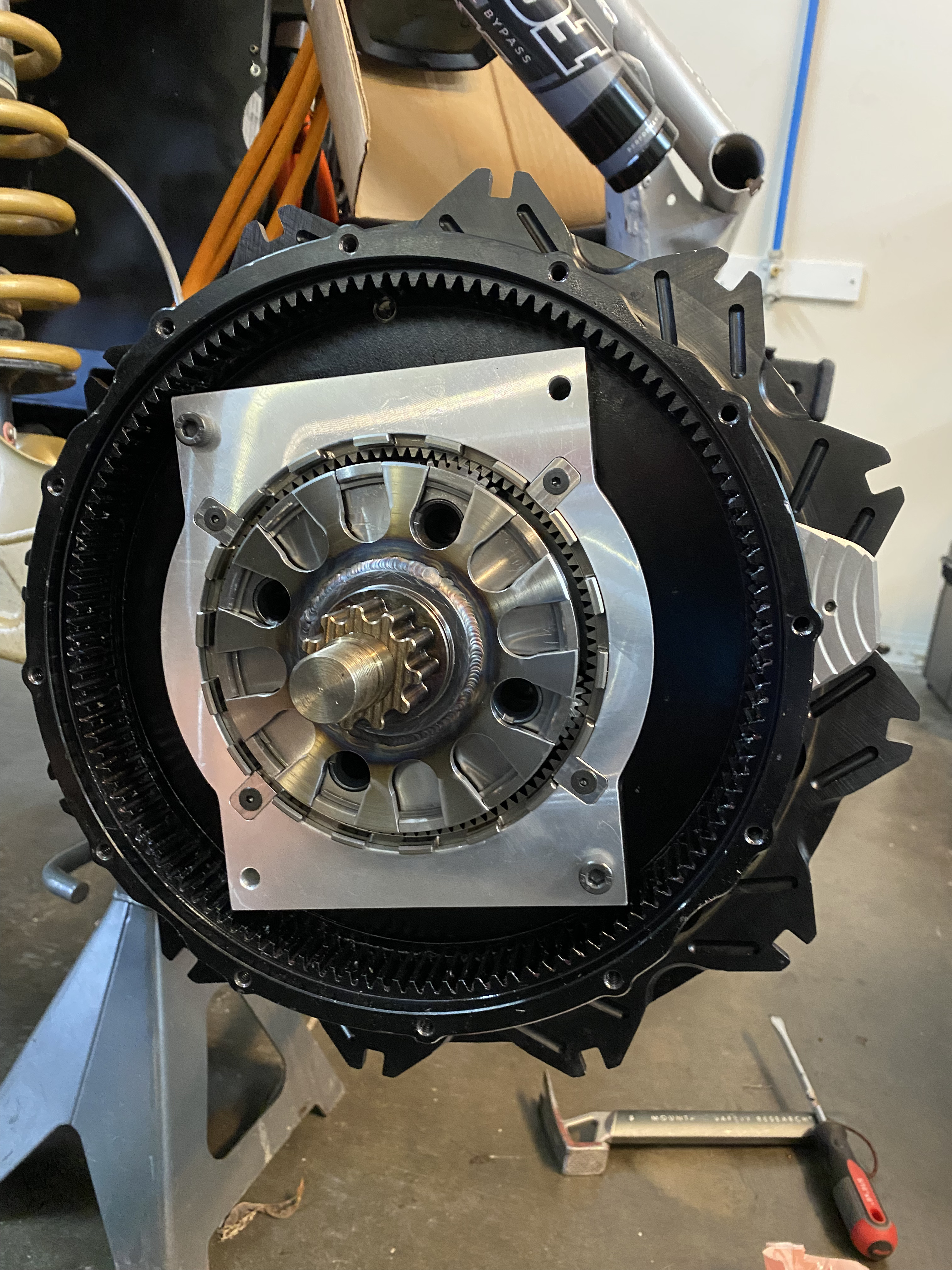
Design Process and Results
- New planetary gearset designed with helical gears
- Quotes showed that custom ring gears were too expensive and had long lead times
- Needed to pivot - a gearset from a junkyard automatic transmission was harvested and retrofitted to the assembly
- Testing with sound level meter proved significant NVH reduction
- Engineer sent from a major automaker from Wolfsburg approved the proof of concept’s NVH, resulting in a contract with the automaker
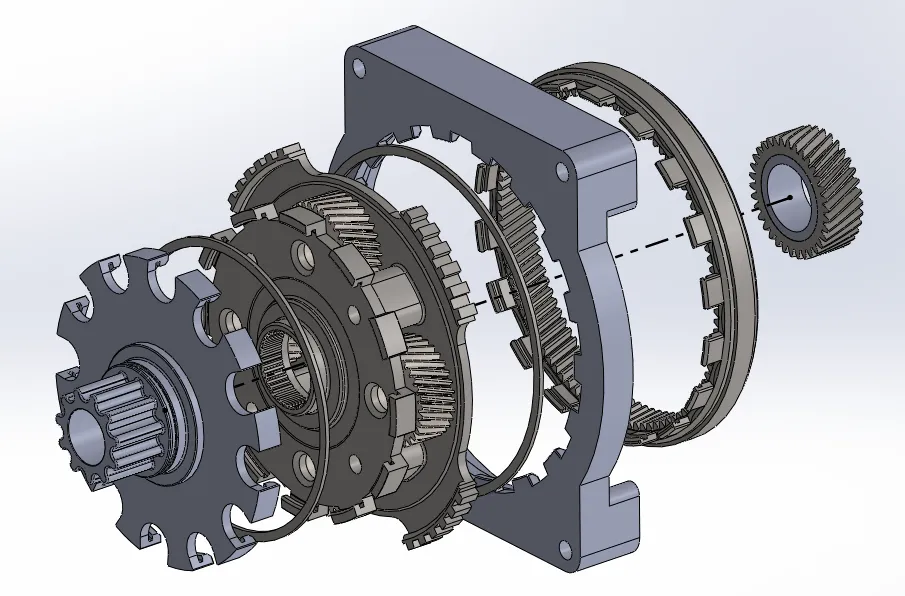
Gearbox, Motor, Brake, and Upright Assembly
Requirements
- Redesign previous assembly, keeping successful design elements and addressing failures
- Small form factor/stack height
- Lightweight
My contribtions
- Redesigned gearset stack - bearings, oiling, gearset selection
- Designed and optimized brake bell (red) with FEA
- Designed integrated upright (orange)
- Redesigned frustum that contains gearset (green)
- Work with machinist to make a printed model
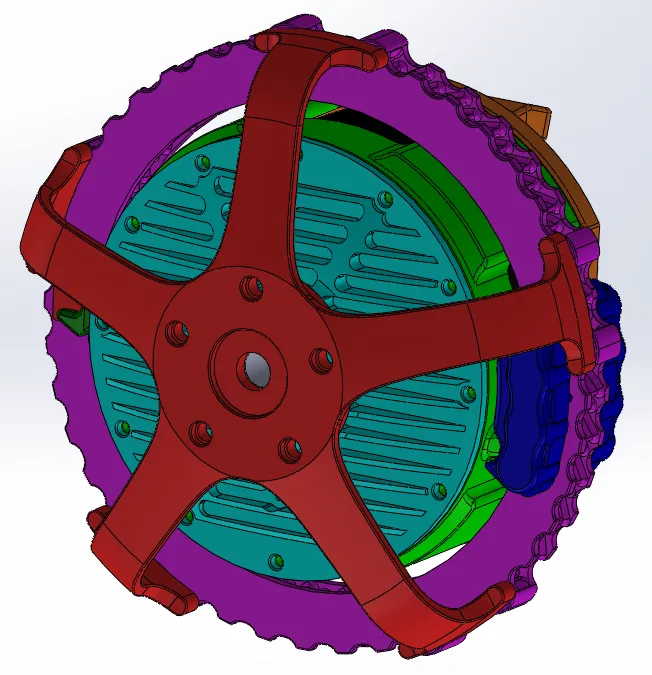
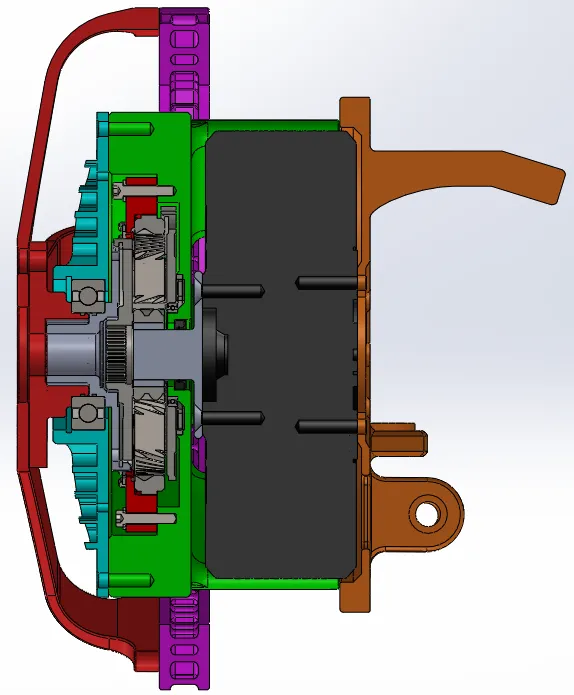
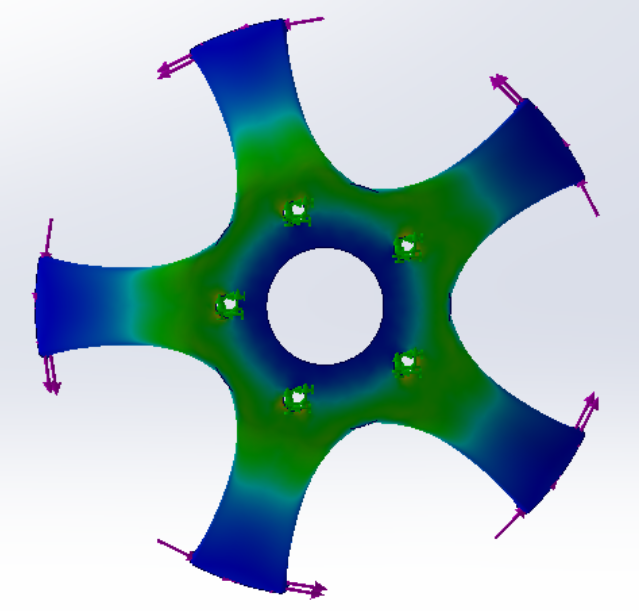
Design Process
Address failures
- Previous bearing solution caused gears to take load from wheels and fail - redesigned to isolate gears from external forces
- New sealing solution designed to stop leaking
Reduce assembly’s stack height and weight
- McLaren MP4-12C upright integrated into motor mount
- Power dense axial flux motor used
- Lightweight brake bell, external rotor/internal caliper setup
- FEA used to optimized brake bell, reducing unsprung and rotating mass
External Brake Rotor/Bell
- Designed and worked closely with machinist to make “bell” to mount external brake rotor
- Mustang GT rotor lightweighted and adapted to function as an external rotor
- Tested at Greening to validate performance vs. original rotor
- Underperformed compared to original rotor, but was significantly lighter
Conclusions
- Promising results, but an equal mass comparison would be more valuable
- Brake rotor cooling optimization needed
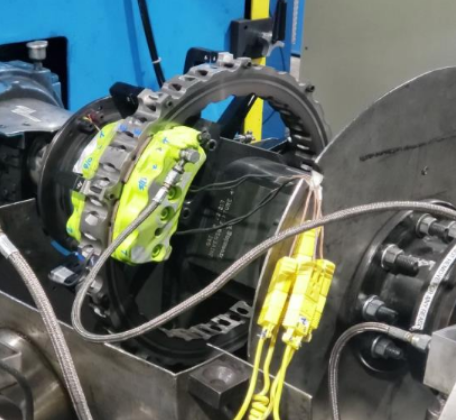
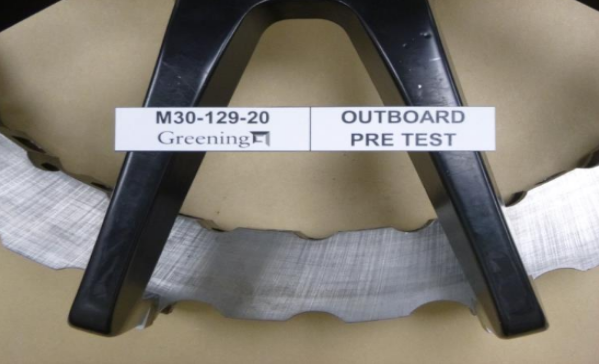
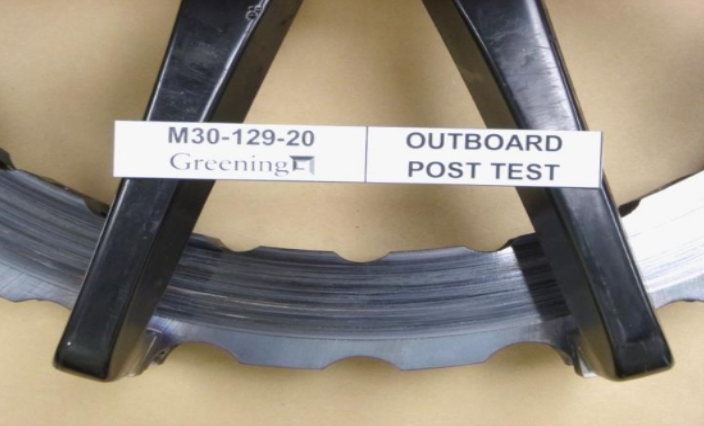
Promaster Van Hybrid Conversion Battery Mounting
Requirements
- Mount to Promaster box truck with minimal modification
- Less than 4 hour assembly time
- Easily installed and removed by non-specialized workers
- Corrosion resistant
Design
- Bolted to truck with 24 nut-serts in 6 locations - holes are already present, no modification needed
- Complete assembly and installation instructions made
- Corrosive resistant materials used for water resistant electronics enclosure and splash guard
- Sheet metal construction allows for easy prototyping and ramp up of production

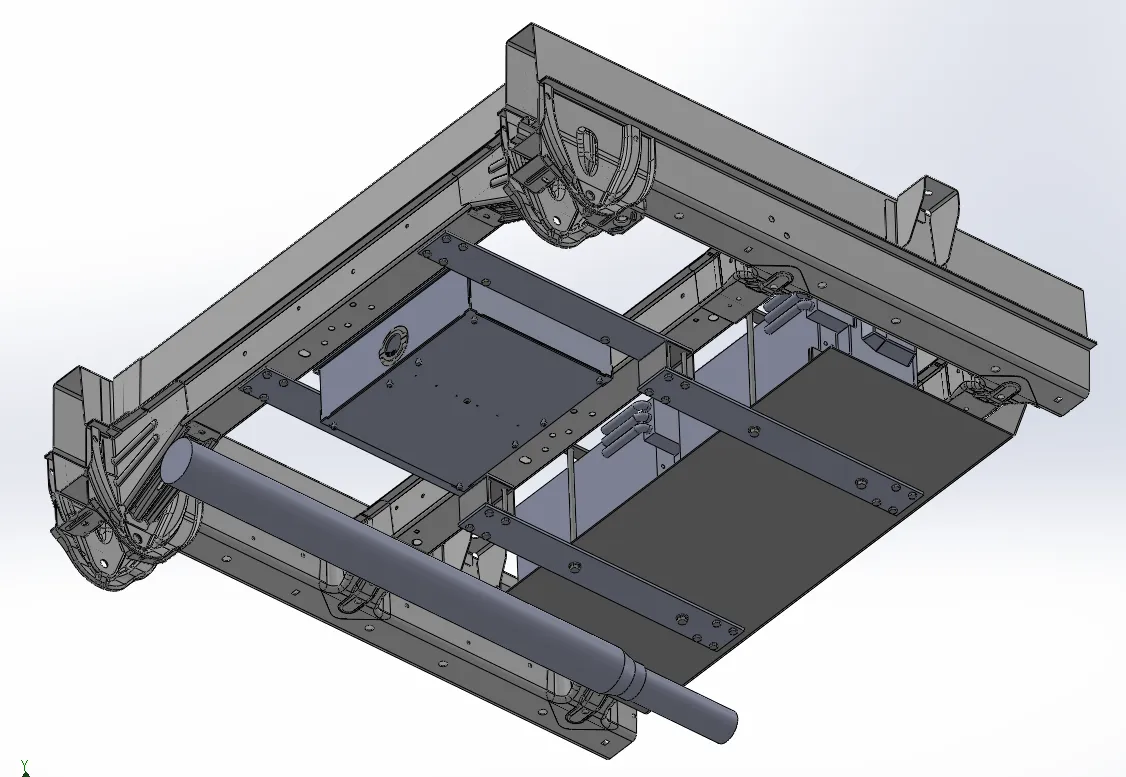
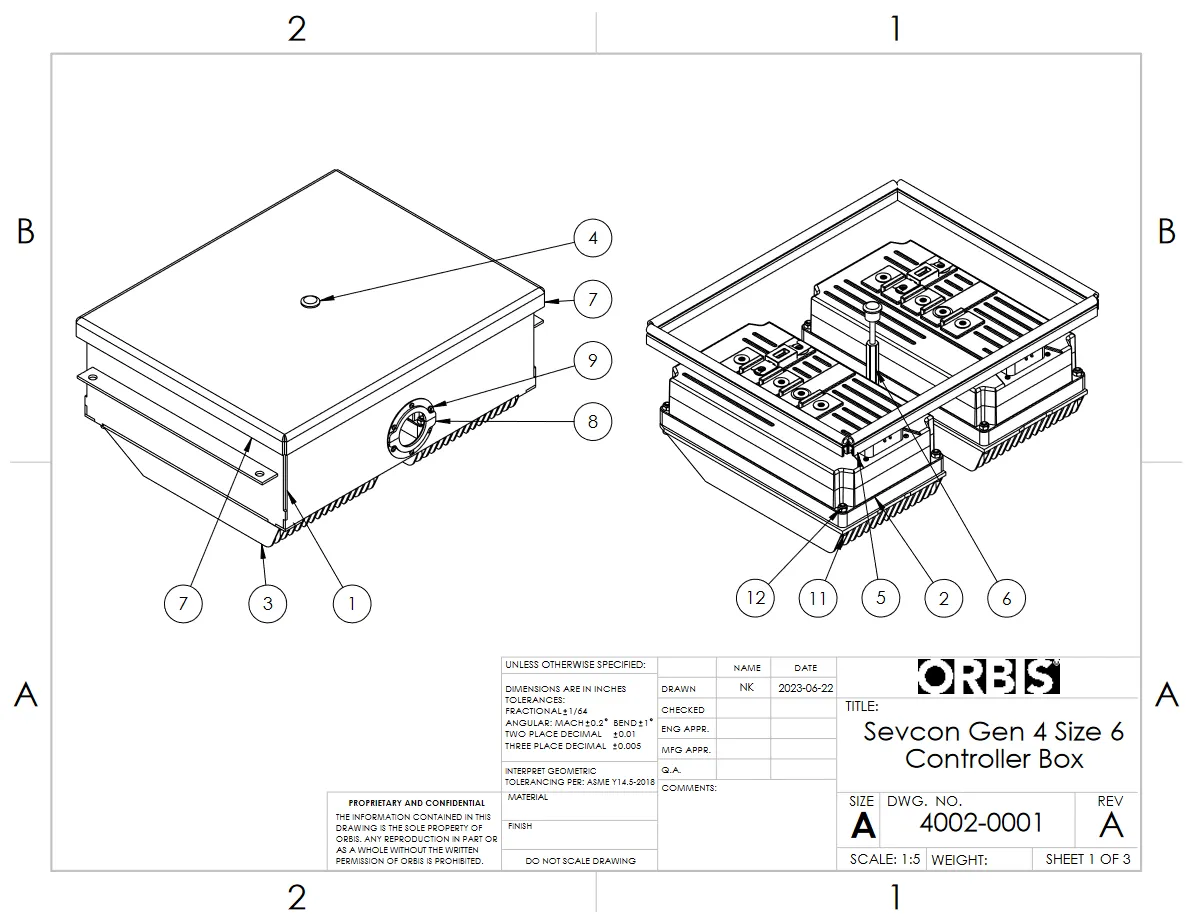
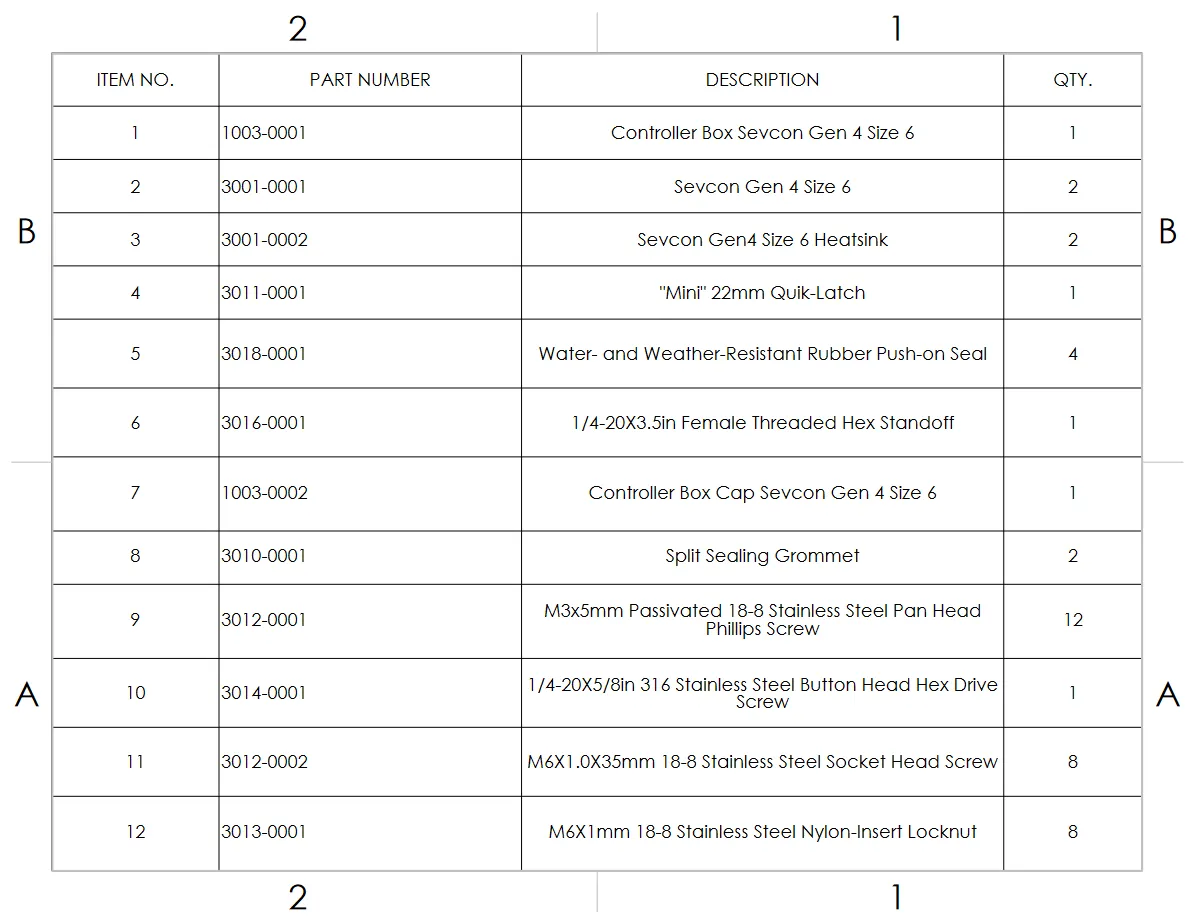
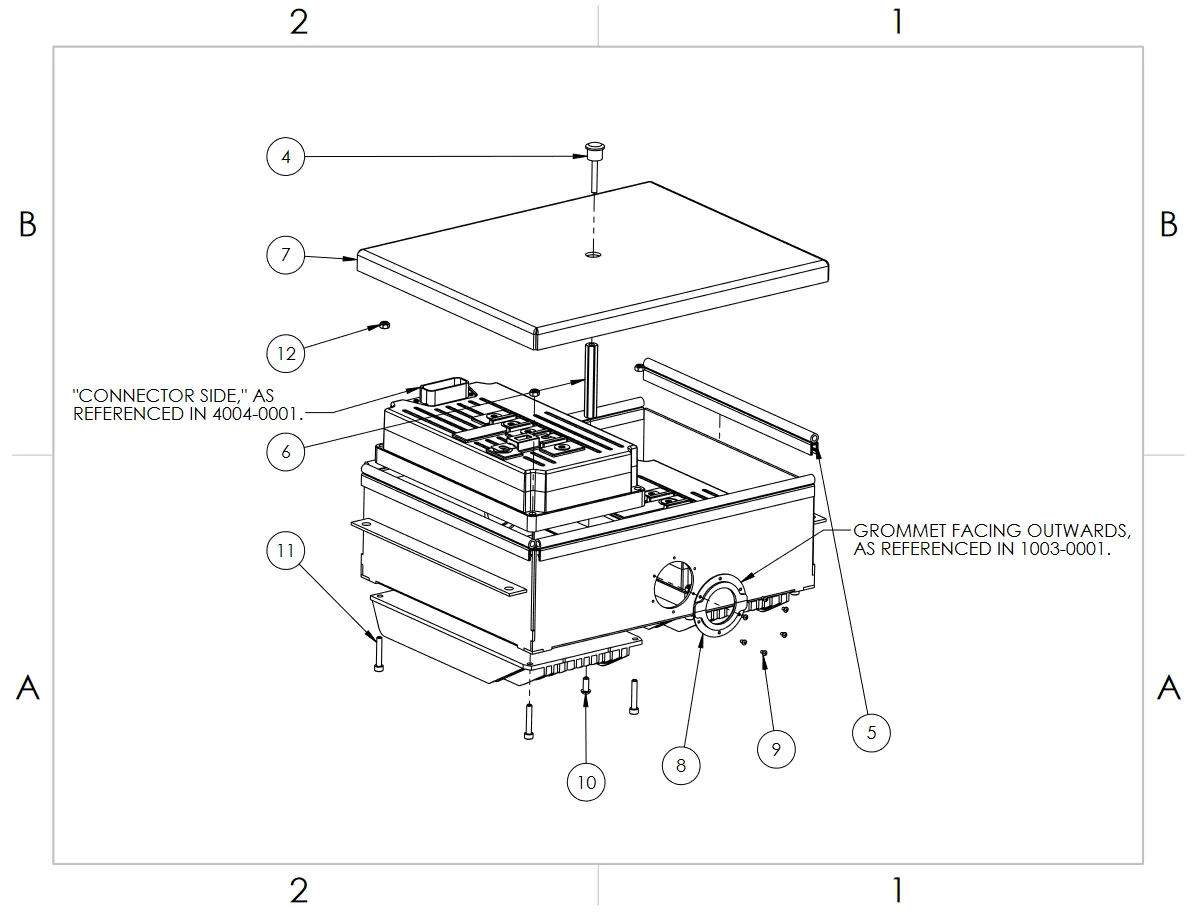
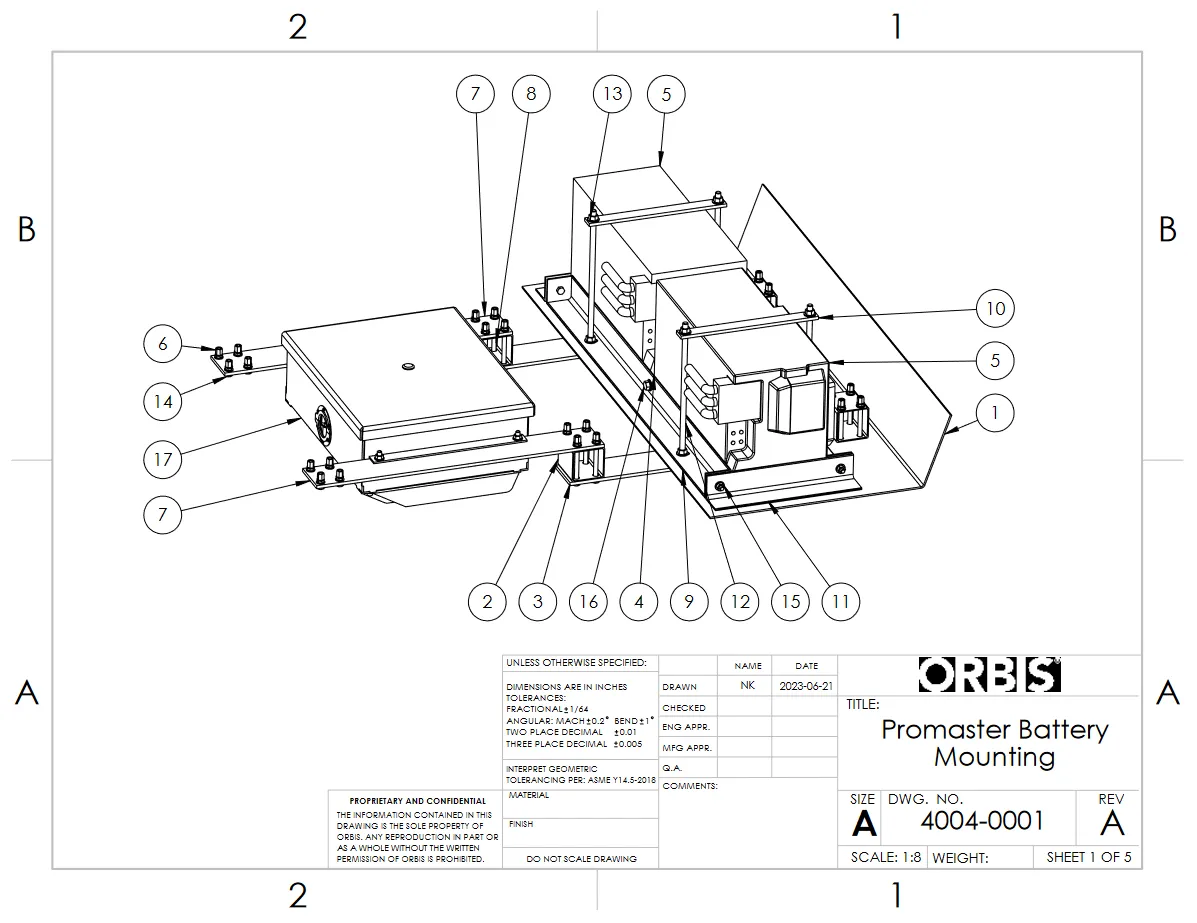
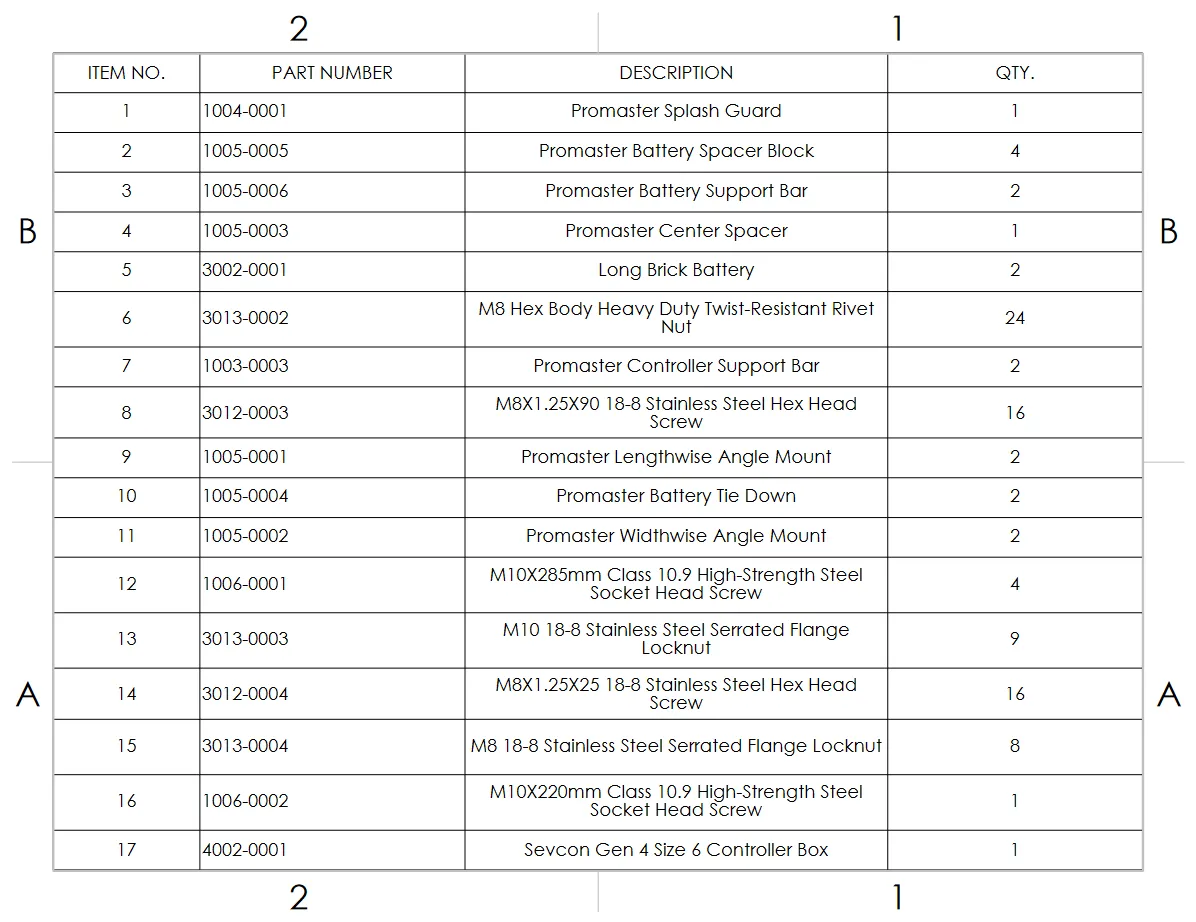
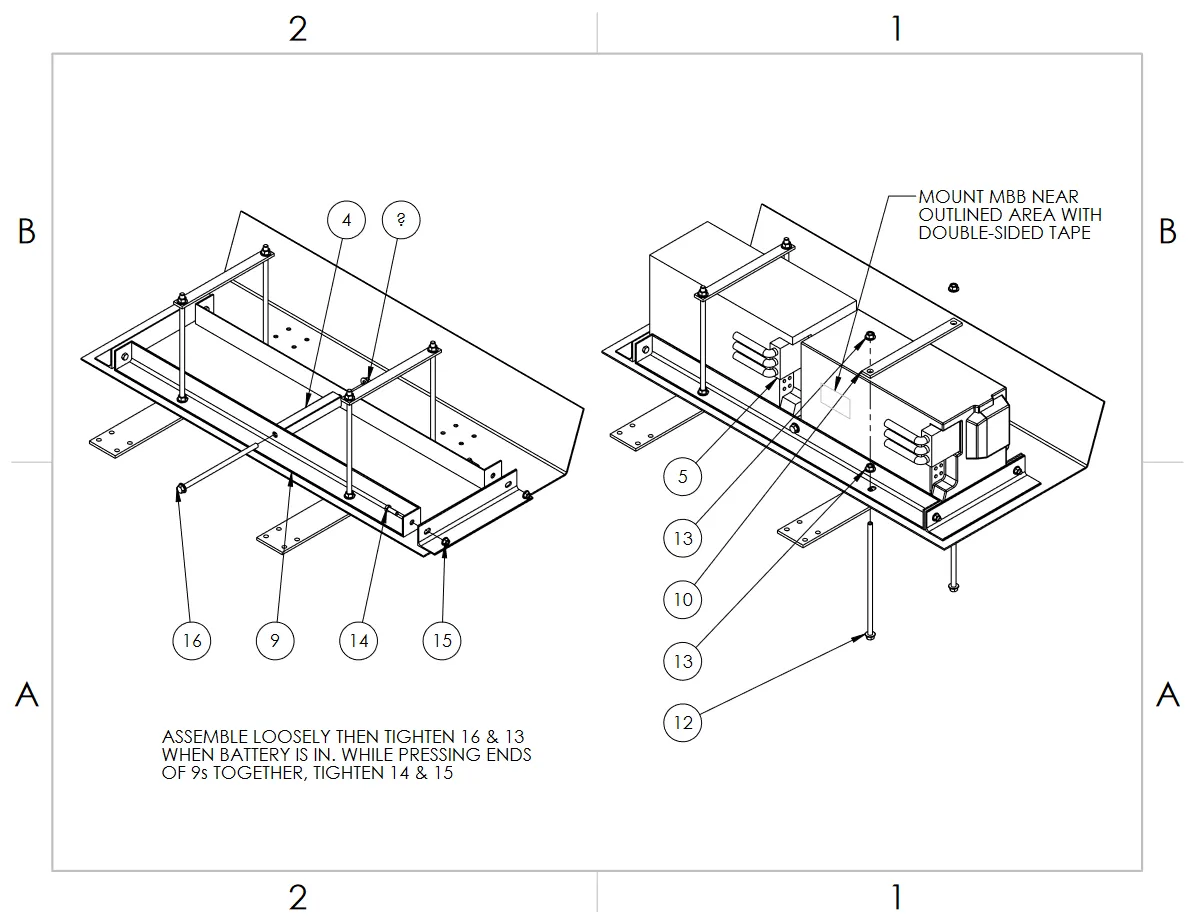
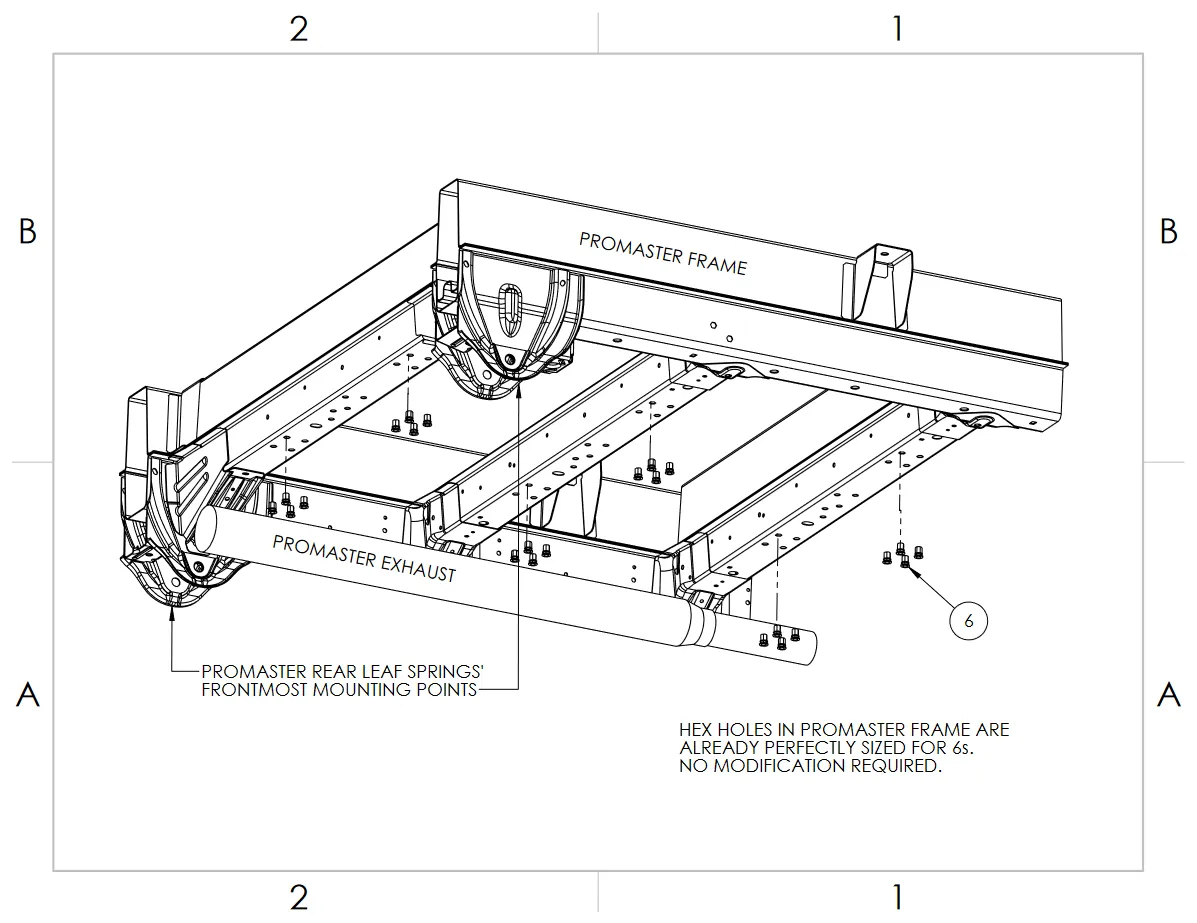
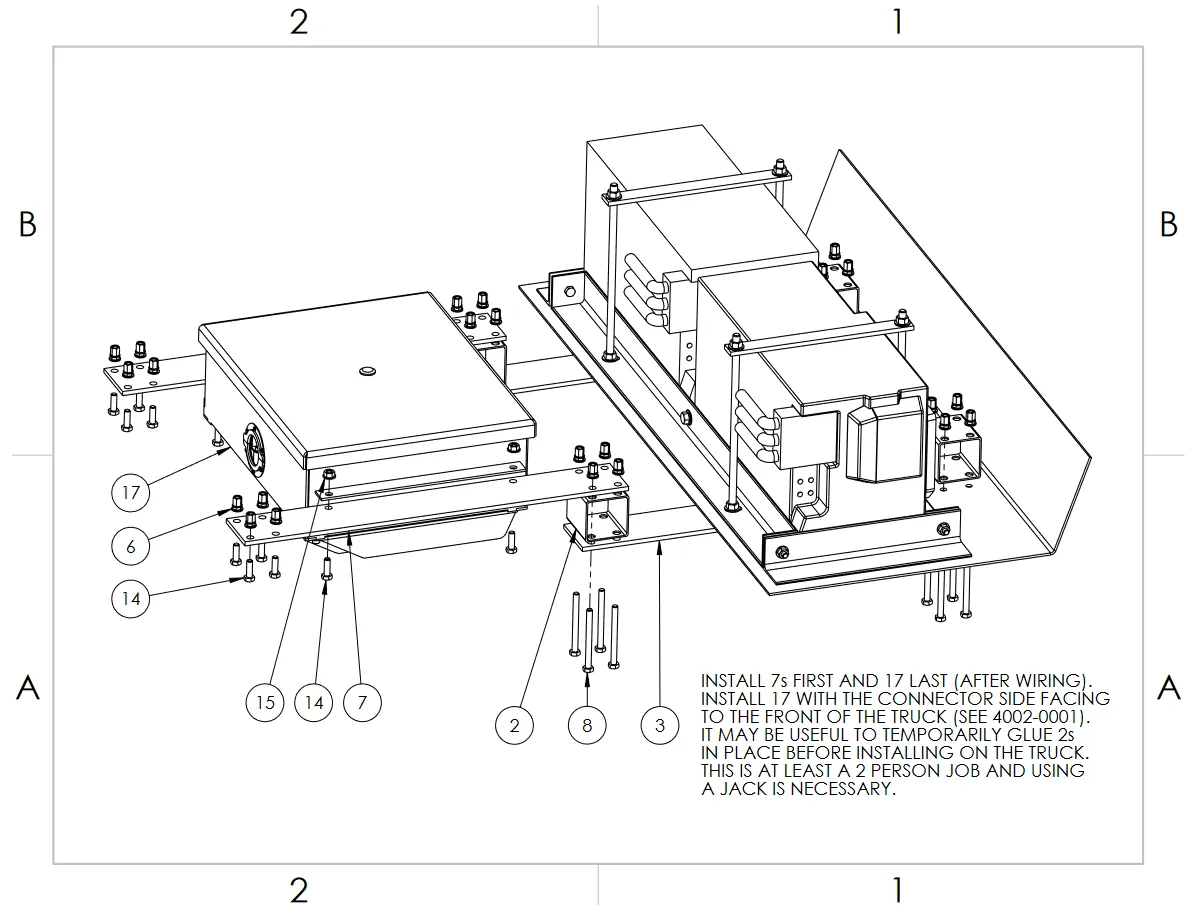